
JVC's Frame Addressing driving method draws images in a single frame at one time to enable the shutter on the 3D glasses for one eye to remain open for an extended period to realise a brighter 3D picture. What's more, this technology incorporates newly developed driving circuitry that helps to drastically improve image brightness. Thanks to JVC's D-ILA driving method, Frame Addressing reproduces more colourful and vivid 3D video content with reduced crosstalk (image overlapping). The DLA-X9000,X7000,X5000 are compatible with a variety of 3D formats including Frame Packing for Blu-ray 3D, Side-by-Side (used mainly for broadcasting), and Top-and-Bottom. These recorded images for the left and right eyes are projected separately on the projector and synchronized, which when viewed by 3D glasses that darken sequentially for each eye, create binocular disparity to enable the brain to perceive them as 3D stereoscopic images. 3D video content is created by using a special camera with two separate lenses that can record images for the left and right eyes sequentially. It will be exciting to see the partnerships and clients refractory metals will bring to 6K.The mechanism behind 3D viewing involves binocular disparity, a unique form of depth perception used by humans that takes two different views and moulds them together into a three-dimensional object. Its proprietary UniMelt system is backed by 18 patents and is the only one like it in the industry. Our powder quality requirements are extremely high and 6K Additive easily cleared that hurdle for us.”ĦK has had a busy last few years, developing new technologies, manufacturing techniques, new partnerships, clients, and many rounds of funding. “Having a reliable, trusted supply chain partner like 6K Additive for refractory materials is critical to our business and to our defense customers. Our tungsten/rhenium powder spheroidized by 6K processed exceptionally well in our selective laser melting machines,” explained Joe Sims, Director of the Quadrus Advanced Manufacturing Division.

“We have a focus on propulsion applications that require high-temperature, high-strength materials used in modern rocket nozzle applications. In the past, the company 3D printed innovative solutions for NASA, being a part of the disruption 3D printing has had on space travel and habitation.Ī 3D printed, non-eroding throat insert for a solid rocket motor nozzle, made by Quadrus Corporation using 6K’s tungsten-rhenium powder.

#Brighter 3d activate full#
We have spheroidized the full spectrum of refractory powders including tantalum, niobium and molybdenum and we are ready to help organizations advance their applications with these materials.”Īlabama-based company Quadrus Corporation is using 6K’s tungsten-rhenium metal powder to 3D print a non-eroding throat insert for a solid rocket motor nozzle. The uniqueness of 6K’s UniMelt ® microwave plasma process, combined with the expertise of our operations team, has allowed us to manufacture production scale volumes for many of the refractory powders like tungsten and tungsten/rhenium. Tungsten has the highest melting point out of all metals at 6,192☏.įrank Roberts, 6K Additive President said “The leading defense organizations are not only looking for refractory materials like tungsten and rhenium, they are looking for it at production scale. This results in high melting points compared to the other metals, such as titanium or nickel.
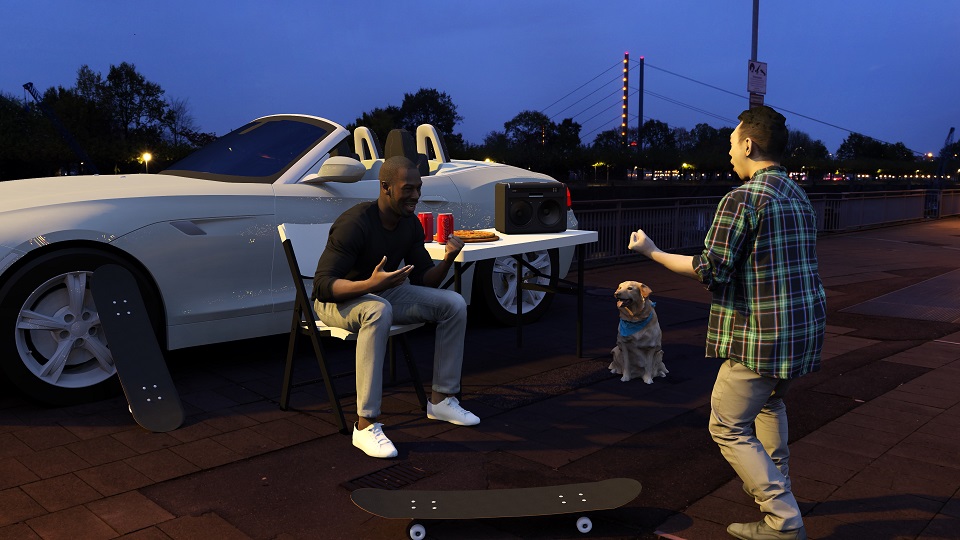
Refractory metals have melting points greater than 3,632☏ and always have three, four, or five electrons in their shells, forming strong covalent bonds with neighboring atoms. The company announced it is now able to use their UniMelt system to manufacture refractory metals such as tungsten, rhenium, and niobutin. Pterodactyls and unicorns soar overhead, yet you are still sitting on your couch, and you can still see your living room and the people around you. Suddenly, the ceiling caves in and you are squinting into the bright, colorful sky of a fantasy world. The system reaches an internal temperature of 6000° Kelvin, the temperature of the surface of the sun, hence the name 6K. The 3D display in the headset makes it look convincing. By combining multiple processes into one this sort of manufacturing cuts time by a few days to a few seconds compared to conventional manufacturing and is able to use scrap metal as feedstock. The UniMelt process uses the fourth phase of matter, plasma, to create a uniform high temperature production zone of four inches in diameter and eight feet long, the machine in its entirety measures 20 feet by 20 feet and can produce 100 tons of material per year. 6K’s UniMelt microwave plasma recycles feedstock into AM-ready metal powder.
